Pressed into Form: An Exploration of Victorian Button Manufacturing Techniques
There's a quiet poetry in holding a Victorian button. More than mere fasteners, they're tiny portals to a bygone era, tangible links to the hands that made them and the garments they adorned. As a collector of many years, I’ve often been captivated not just by their beauty and rarity, but by the very process of their creation – a journey that combined burgeoning industrial innovation with enduring artisanal skill. This article delves into the manufacturing techniques employed during the Victorian period, offering a deeper appreciation for these miniature masterpieces.
The Victorian era (roughly 1837-1901) witnessed a dramatic shift in button production. Prior to this time, buttons were largely handcrafted, a laborious process often undertaken by individuals or small workshops. The burgeoning Industrial Revolution, however, brought about a demand for more affordable and readily available buttons, prompting significant changes in manufacturing approaches.
The Rise of Stamping: Mechanizing the Form
The earliest significant advance was the development of button stamping. Before stamping, buttons were commonly turned on a lathe, a time-consuming method ideal for bespoke, high-end pieces. Stamping, however, allowed for the relatively rapid production of simple, symmetrical buttons. The process began with a flat disc of material - horn, bone, shell, or metal - which was then forced through a die using a powerful press. The die, a precision-engineered tool, imparted the desired button shape. Early stamping machines were often powered by steam, a powerful symbol of the era's technological advancements.
While stamping revolutionized production, it also brought limitations. Early stamping processes primarily produced flat or slightly concave buttons, lacking the intricate details we often associate with Victorian buttons. The design of the dies was critical, and skilled toolmakers were highly valued. The quality of the stamping directly impacted the button’s strength and appearance – flaws in the die resulted in imperfections in the button itself. A telltale sign of stamped buttons is often a slight “lip” or unevenness around the edge.
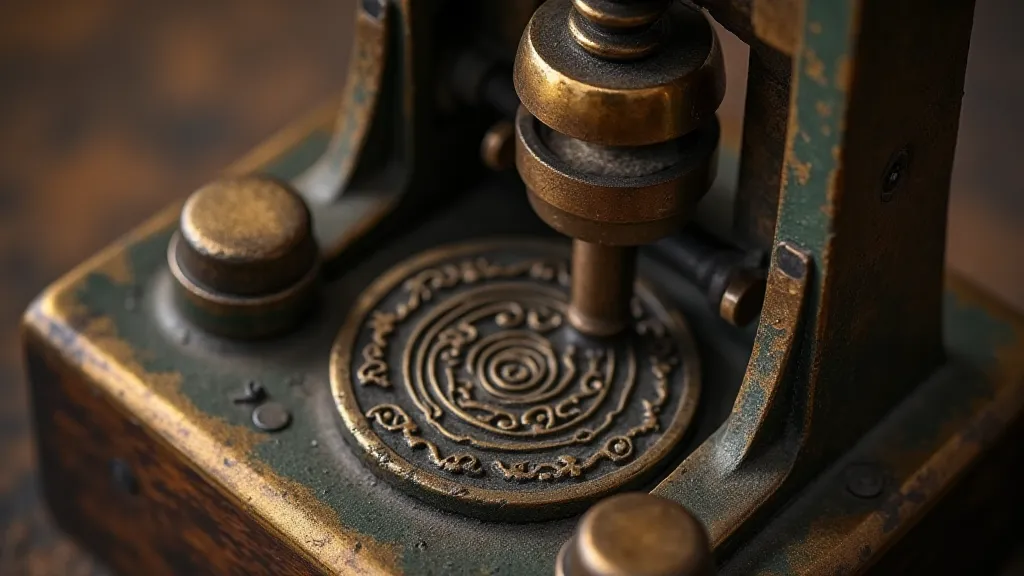
Molding: Achieving Three-Dimensional Beauty
The next significant step was the development of button molding. This process allowed for the creation of three-dimensional buttons with raised designs and intricate details – a stark contrast to the relatively flat buttons produced by early stamping techniques. The molding process typically involved injecting a pliable material, such as gutta-percha (a natural latex-like substance popular in the mid-19th century), or vulcanized rubber into a mold cavity. Once the material hardened, the mold was opened, revealing the button in its final shape.
The complexity of molded buttons was directly tied to the sophistication of the molds themselves. These molds were often crafted from multiple pieces, allowing for incredibly detailed designs to be reproduced. The skill required to create these molds was truly remarkable. Gutta-percha and vulcanized rubber offered a degree of flexibility that enabled complex forms, but they also had limitations in terms of durability and longevity. Buttons made from these materials are often brittle and prone to cracking.
The rise of molded buttons coincided with the height of Victorian design trends – a period characterized by elaborate ornamentation and a love of naturalistic motifs. I remember finding a small, intricately molded gutta-percha button depicting a hummingbird, its wings delicately rendered. Holding it, I felt a profound connection to the artisan who poured their skill and creativity into such a tiny object.
The Art of Hand-Finishing: Adding the Final Touches
While stamping and molding were pivotal in mass production, the Victorian button wasn't solely the product of machinery. A crucial element was hand-finishing. Even after a button had been stamped or molded, it almost invariably underwent further refinement by hand. This could involve smoothing rough edges, applying decorative coatings (like gold or silver leaf), painting intricate designs, or even meticulously adding hand-painted details.
Consider the prevalence of jet buttons during the Victorian era, particularly after the death of Prince Albert. These buttons, crafted from fossilized wood, were often painstakingly hand-polished to achieve a deep, lustrous black. The skill in achieving that perfect, mirror-like finish was a mark of a truly accomplished artisan. Similarly, hand-painting techniques allowed for the creation of astonishingly realistic floral and animal designs on button surfaces.
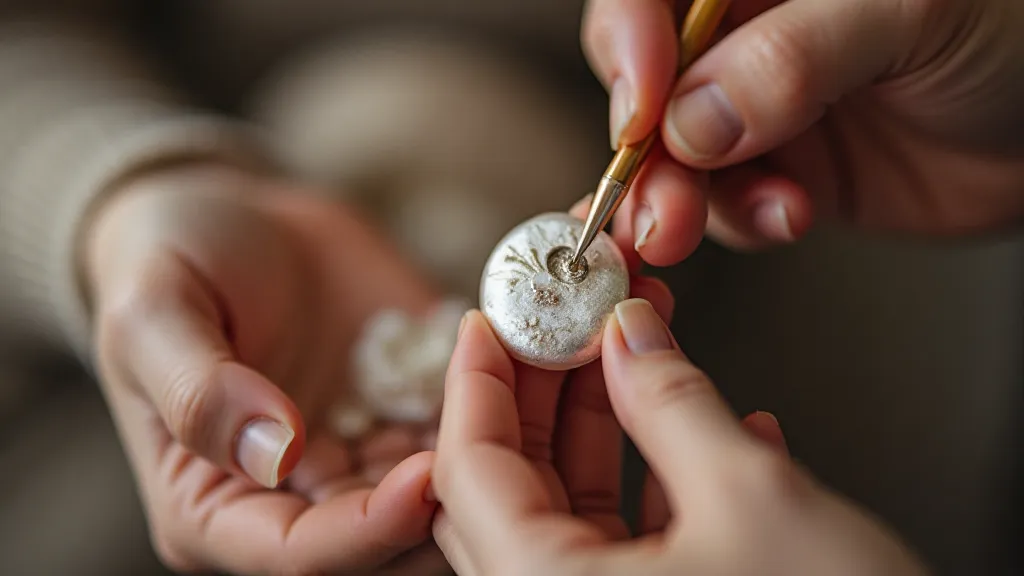
Materials and Their Manufacturing Implications
The material used for a button had a profound impact on the manufacturing processes employed. Horn buttons, for instance, were relatively inexpensive and readily available, making them suitable for mass production via stamping. Mother-of-pearl buttons, prized for their iridescence, required a more delicate approach – often involving a combination of stamping, molding, and meticulous hand-polishing to reveal their full beauty. Jet buttons, as mentioned earlier, demanded careful polishing to enhance their characteristic dark luster.
The advent of early button factories further concentrated production and fueled innovation. These factories, often located in industrial centers like Birmingham in England and Providence in the United States, brought together skilled artisans and advanced machinery under one roof. Documents from these factories – scarce as they are – paint a picture of a complex and highly organized process, from raw material acquisition to finished product distribution. Some early button factories experimented with new materials like celluloid (an early plastic), further expanding the range of button designs and manufacturing techniques.
The Legacy of Victorian Button Craftsmanship
Today, the appreciation for Victorian buttons extends far beyond their use as mere fasteners. They are cherished for their historical significance, their artistic merit, and the tangible connection they offer to a bygone era. Examining the manufacturing techniques employed in their creation provides a deeper understanding of the ingenuity and skill of Victorian artisans. The combination of technological innovation and artisanal expertise resulted in a uniquely beautiful and enduring legacy.
The quiet clink of a Victorian button in your hand – a sound so unassuming, yet so evocative of the past. It's a testament to the dedication and artistry of the individuals who pressed these miniature works of art into form.
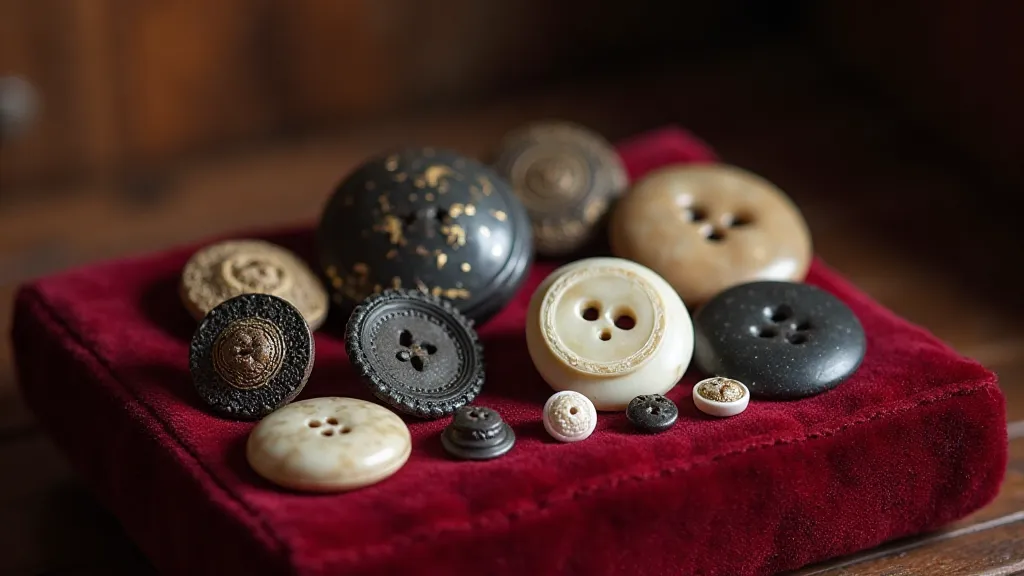